صنعت ساختمان سازی پیوسته در حال تحول است و استفاده از مصالح نوین با ویژگی های برتر اهمیت فزاینده ای یافته است. در این میان بلوک های سبک به دلیل مزایایی چون کاهش بار مرده ساختمان بهبود عملکرد عایق بندی حرارتی و صوتی و سرعت اجرای بالاتر جایگاه ویژه ای پیدا کرده اند. بلوک پوکه ای یکی از پرکاربردترین انواع بلوک سبک در ایران است که ماده اصلی تشکیل دهنده آن پوکه معدنی است.
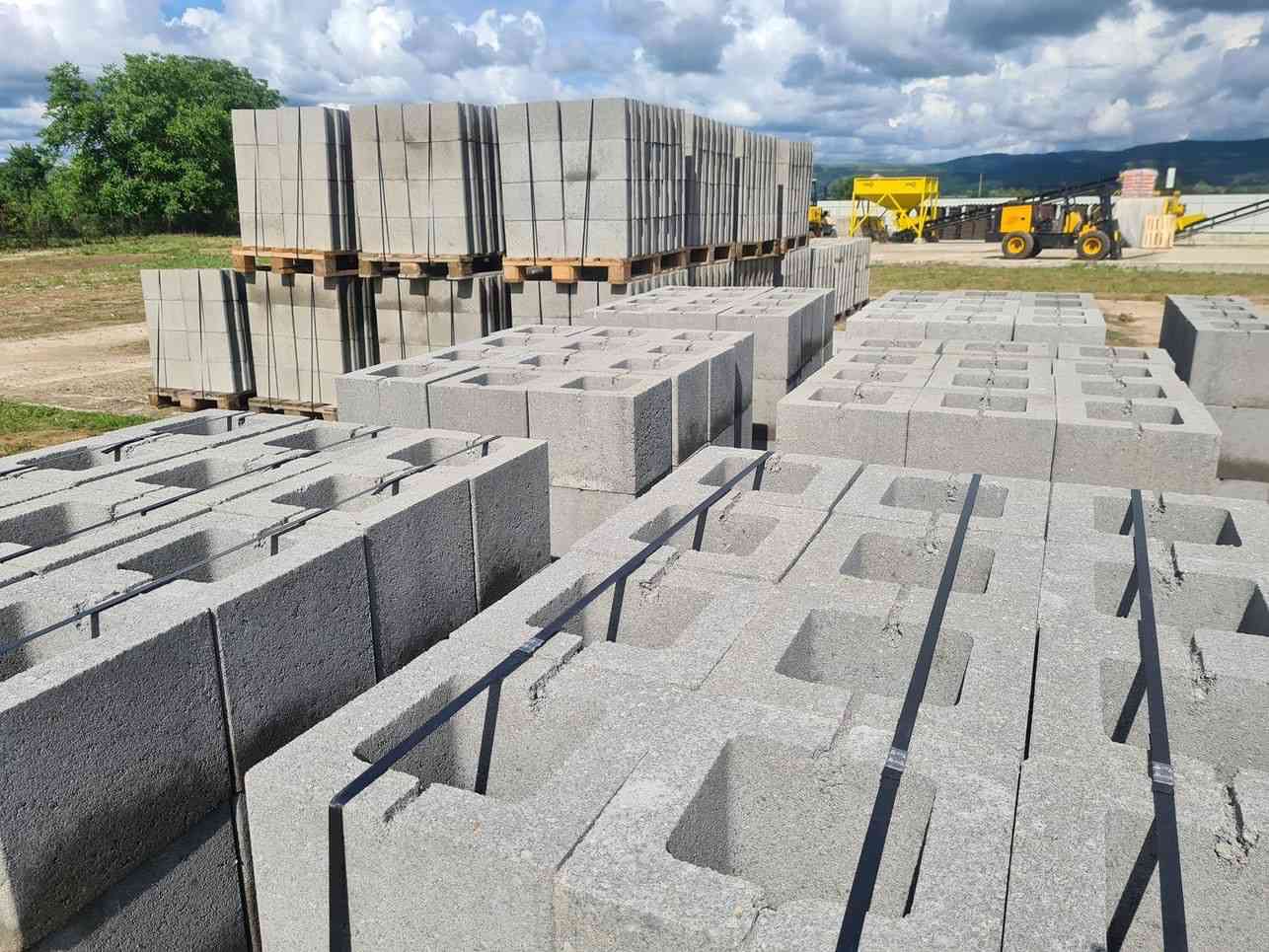
تولید بلوک پوکه ای با کیفیت و استاندارد نیازمند دانش و دقت فراوان است. قلب تپنده فرآیند تولید این بلوک ها «طرح اختلاط» یا نسبت دقیق و علمی مواد اولیه با یکدیگر است. یک طرح اختلاط مناسب نه تنها مقاومت و دوام بلوک را تضمین می کند بلکه بر وزن نهایی جذب آب و سایر خصوصیات فیزیکی و مکانیکی آن نیز تأثیر مستقیم دارد. این راهنمای جامع به تفصیل به بررسی اصول و مراحل تهیه طرح اختلاط بلوک پوکه ای می پردازد تا تولیدکنندگان بتوانند بلوک هایی با بالاترین کیفیت و کارایی تولید کنند و از مشکلات رایج در این صنعت پیشگیری نمایند.
چرا طرح اختلاط بلوک پوکه ای مهم است؟
پوکه معدنی سنگ آذرین متخلخلی است که به دلیل وزن سبک ساختار سلولی و خواص عایق بندی طبیعی یکی از بهترین مصالح برای تولید بلوک های سبک محسوب می شود. با این حال خواص منحصر به فرد پوکه تنها زمانی به بلوک نهایی منتقل می شود که با سایر اجزا یعنی سیمان و آب به نسبت های صحیح و با روشی علمی ترکیب گردد.
اهمیت طرح اختلاط بلوک پوکه ای از آنجا ناشی می شود که این ترکیب مستقیماً بر خصوصیات حیاتی بلوک تأثیر می گذارد. نسبت های نادرست می تواند منجر به مشکلات جدی شود.
- کاهش مقاومت فشاری: بلوک نمی تواند بارهای وارده را تحمل کند.
- افزایش جذب آب: بلوک در برابر رطوبت آسیب پذیر می شود و خواص عایق بندی خود را از دست می دهد.
- ترک خوردگی و انقباض: به دلیل نسبت نامناسب آب به سیمان یا دانه بندی نامنظم پوکه.
- وزن غیر استاندارد: بلوک بیش از حد سنگین یا سبک می شود.
- مشکلات در فرآیند تولید: ملات چسبندگی کافی نداشته یا بیش از حد روان است.
بنابراین طرح اختلاط دقیق ستون فقرات تولید بلوک پوکه ای با کیفیت است و تضمین کننده مطابقت محصول نهایی با استانداردهای ملی و بین المللی و همچنین نیازهای پروژه ساختمانی است.توجه به تفاوتهای طرح اختلاط بلوک پوکهای با بلوک لیکا از نظر ترکیبات و کاربرد برای انتخاب صحیح مصالح ضروری است.
مواد اولیه مورد نیاز برای طرح اختلاط بلوک پوکه ای
تولید بلوک پوکه ای نیازمند انتخاب دقیق و ترکیب صحیح چند ماده اولیه اصلی است. کیفیت و ویژگی های هر یک از این مواد به شدت بر کیفیت بلوک نهایی تأثیرگذار است.
- پوکه معدنی (در اندازه های مختلف): به عنوان سنگدانه سبک و پرکننده اصلی.
- سیمان: به عنوان چسباننده و عامل اصلی ایجاد مقاومت.
- آب: برای فعال کردن سیمان و ایجاد کارایی در ملات.
- مواد افزودنی (اختیاری برای بهبود خواص بلوک): شامل روان کننده ها دیرگیرکننده ها زودگیرکننده ها مواد حباب ساز یا حباب پوش و مواد آب بند کننده.
شناخت دقیق ویژگی های هر یک از این مواد و تأثیر آن ها در طرح اختلاط برای دستیابی به یک نتیجه مطلوب ضروری است.
انواع پوکه معدنی مورد استفاده در بلوک پوکه ای
پوکه معدنی محصول فعالیت های آتشفشانی است و در مناطق مختلف ایران با کیفیت ها و دانه بندی های متفاوتی یافت می شود. انتخاب نوع و اندازه پوکه یکی از تصمیمات کلیدی در طرح اختلاط است.
به طور کلی پوکه مورد استفاده در بلوک زنی باید دارای ویژگی های زیر باشد:
- وزن مخصوص پایین: برای دستیابی به بلوک سبک.
- مقاومت کافی: برای تحمل فرآیند تولید و بارهای وارده در سازه.
- جذب آب مناسب: نه بیش از حد بالا که باعث مصرف زیاد سیمان و مشکلات کیورینگ شود و نه بیش از حد پایین که اختلاط را دشوار کند.
- دانه بندی مناسب: توزیع اندازه ذرات باید به گونه ای باشد که فضای خالی بین آن ها به حداقل برسد و نیاز به سیمان کاهش یابد.
- عاری از مواد مضر: مانند رس مواد آلی سولفات ها و کلریدها که می توانند بر گیرش سیمان و دوام بلوک تأثیر منفی بگذارند.
انواع رایج پوکه بر اساس اندازه دانه بندی عبارتند از:
- پوکه ماسه ای (۰-۵ میلی متر): برای پر کردن فضاهای خالی بین دانه های درشت تر و ایجاد سطحی صاف تر.
- پوکه عدسی (۵-۱۰ میلی متر): اندازه متوسط پرکاربرد در بلوک های دیواری و تیغه ای.
- پوکه نخودی (۱۰-۲۰ میلی متر): دانه های درشت تر ممکن است در بلوک های سایز بزرگ یا کاربردهای خاص استفاده شود.
معمولاً برای تولید بلوک پوکه ای ترکیبی از پوکه با دانه بندی های مختلف (مثلاً ماسه ای و عدسی) استفاده می شود تا دانه بندی مطلوب و متراکم تری حاصل شود که این امر به کاهش مصرف سیمان و بهبود خواص بلوک کمک می کند. انجام آزمایش دانه بندی پوکه قبل از استفاده برای تعیین نسبت های صحیح در طرح اختلاط ضروری است.
نقش سیمان در طرح اختلاط بلوک پوکه ای
سیمان چسباننده ای هیدرولیکی است که با واکنش با آب خمیری ایجاد می کند که دانه های پوکه را به یکدیگر متصل کرده و پس از گیرش و سخت شدن مقاومت و پایداری بلوک را تأمین می نماید. نوع و مقدار سیمان مصرفی یکی از اصلی ترین عوامل تعیین کننده مقاومت نهایی بلوک پوکه ای است.
معمولاً برای تولید بلوک پوکه ای از سیمان پرتلند تیپ ۲ استفاده می شود که برای شرایط عمومی آب و هوایی مناسب است. در مناطق با آب و هوای سردتر یا نیاز به مقاومت اولیه سریع تر ممکن است از سیمان تیپ ۱ یا سیمان های زودگیر استفاده شود اما باید به سرعت گیرش بالا و تولید حرارت بیشتر در این سیمان ها توجه کرد. در محیط های مهاجم سولفاتی استفاده از سیمان تیپ ۵ یا سیمان های ضد سولفات توصیه می شود.
مقدار سیمان در طرح اختلاط بلوک پوکه ای باید به اندازه ای باشد که پوشش کافی برای تمام دانه های پوکه فراهم کند و فضای خالی بین آن ها را پر نماید تا پس از هیدراسیون ساختاری متراکم و مقاوم ایجاد شود. کمبود سیمان منجر به بلوک های ضعیف و پودری می شود در حالی که مصرف بیش از حد سیمان اگرچه مقاومت را افزایش می دهد اما می تواند باعث افزایش وزن بلوک ترک خوردگی ناشی از انقباض و افزایش هزینه تولید شود.
نسبت آب به سیمان (W/C Ratio) نیز در بلوک پوکه ای بسیار حیاتی است. این نسبت بر کارایی ملات تازه و مقاومت نهایی بتن سخت شده تأثیر می گذارد. در تولید بلوک معمولاً از بتن با اسلامپ (روانی) بسیار پایین استفاده می شود بنابراین نسبت آب به سیمان نیز نسبتاً پایین است. کنترل دقیق میزان آب با در نظر گرفتن رطوبت موجود در پوکه برای دستیابی به طرح اختلاط بهینه ضروری است.
مراحل تعیین طرح اختلاط بلوک پوکه ای
تعیین طرح اختلاط بلوک پوکه ای یک فرآیند علمی است که نیازمند رویکردی سیستماتیک و انجام آزمایش های کنترلی است. هدف یافتن بهینه ترین ترکیب مواد اولیه برای دستیابی به بلوکی است که هم از نظر خواص فیزیکی و مکانیکی (مانند مقاومت وزن جذب آب) و هم از نظر اقتصادی (مصرف بهینه مواد) مطلوب باشد.
مراحل کلی تعیین طرح اختلاط به شرح زیر است:
- تعیین هدف و الزامات بلوک
- انتخاب و آزمایش مواد اولیه مناسب
- تعیین نسبت های اولیه مواد
- انجام مخلوط های آزمایشی (Trial Mixes)
- تولید بلوک های آزمایشی و آزمایش آن ها
- اصلاح طرح اختلاط در صورت نیاز
این فرآیند تکراری تضمین کننده تولید بلوکی با کیفیت پایدار و مطابق با استانداردها است.
نکات مهم در طرح اختلاط بلوک پوکه ای
علاوه بر رعایت مراحل علمی تعیین طرح اختلاط توجه به نکات اجرایی و کیفی در فرآیند تولید نیز برای موفقیت بسیار مهم است.
- استفاده از آب تمیز و بدون املاح: آب مصرفی نباید حاوی مقادیر زیادی سولفات کلرید قند روغن یا مواد آلی باشد که می توانند بر فرآیند هیدراسیون سیمان و مقاومت نهایی تأثیر منفی بگذارند.
- اختلاط کامل مواد اولیه: مواد باید به صورت یکنواخت و همگن در میکسر مخلوط شوند تا سیمان به خوبی تمام دانه های پوکه را بپوشاند و خمیر سیمان به صورت یکنواخت در مخلوط پخش شود. زمان و ترتیب افزودن مواد به میکسر نیز اهمیت دارد. معمولاً ابتدا مقداری آب و سیمان مخلوط شده سپس پوکه و بقیه آب اضافه می شود.
- رعایت نسبت های دقیق مواد اولیه: وزن کردن یا پیمانه کردن دقیق مواد طبق طرح اختلاط تعیین شده حیاتی است. هرگونه انحراف از نسبت ها می تواند خواص بلوک نهایی را تحت تأثیر قرار دهد. استفاده از تجهیزات اندازه گیری کالیبره شده توصیه می شود.
- کیورینگ مناسب بلوک ها: پس از تولید بلوک ها باید تحت شرایط مناسب رطوبت و دما عمل آوری (کیورینگ) شوند. کیورینگ فرآیند حیاتی برای ادامه هیدراسیون سیمان و کسب مقاومت نهایی است. عدم کیورینگ مناسب می تواند باعث کاهش مقاومت افزایش جذب آب و ترک خوردگی شود. روش های کیورینگ شامل پوشاندن بلوک ها با نایلون پاشش آب و یا استفاده از اتاق های بخار (برای کیورینگ تسریع شده) است.
- کنترل رطوبت پوکه: پوکه معدنی معمولاً دارای رطوبت طبیعی است که باید در محاسبه میزان آب مورد نیاز برای اختلاط لحاظ شود. نادیده گرفتن رطوبت پوکه می تواند نسبت آب به سیمان را تغییر داده و بر کیفیت ملات و بلوک تأثیر بگذارد.
- ویبره مناسب هنگام قالب گیری: در دستگاه بلوک زنی اعمال ویبره کافی و مناسب برای متراکم کردن ملات در قالب و حذف حباب های هوا ضروری است. ویبره بیش از حد نیز می تواند باعث تفکیک دانه ها شود.
تاثیر رطوبت در طرح اختلاط بلوک پوکه ای
رطوبت موجود در پوکه معدنی یکی از عوامل مهمی است که اغلب در فرآیند تولید بلوک پوکه ای نادیده گرفته می شود اما تأثیر قابل توجهی بر طرح اختلاط و کیفیت نهایی بلوک دارد.
پوکه معدنی به دلیل ساختار متخلخل خود می تواند مقداری آب را در خود نگه دارد. این رطوبت بخشی از آب مورد نیاز برای هیدراسیون سیمان را تأمین می کند و در عین حال بر کارایی ملات تازه تأثیر می گذارد. اگر میزان رطوبت پوکه قبل از اختلاط اندازه گیری نشود و در محاسبه کل آب مورد نیاز لحاظ نگردد نسبت واقعی آب به سیمان در مخلوط تغییر خواهد کرد.
برای مثال اگر پوکه رطوبت بالایی داشته باشد و شما مقدار آب اضافه شده به مخلوط را بدون در نظر گرفتن این رطوبت محاسبه کنید نسبت آب به سیمان عملاً بالاتر از حد مطلوب خواهد بود. این امر می تواند منجر به کاهش مقاومت فشاری افزایش تخلخل و مشکلات در فرآیند قالب گیری و کیورینگ شود.
برعکس اگر رطوبت پوکه کم باشد و آب کافی به مخلوط اضافه نشود نسبت آب به سیمان پایین تر از حد نیاز می شود. این وضعیت باعث کاهش کارایی ملات دشواری در اختلاط و تراکم و هیدراسیون ناقص سیمان و در نتیجه کاهش مقاومت بلوک خواهد شد.
بنابراین اندازه گیری دقیق رطوبت پوکه (و در صورت استفاده سایر سنگدانه ها) قبل از هر نوبت تولید یک گام ضروری در کنترل کیفیت است. با دانستن میزان رطوبت پوکه می توان مقدار آب اضافه شده به میکسر را تنظیم کرد تا نسبت آب به سیمان ثابت و مطابق با طرح اختلاط بهینه حفظ شود.
تجهیزات مورد نیاز برای تولید بلوک پوکه ای
تولید بلوک پوکه ای در مقیاس صنعتی یا نیمه صنعتی نیازمند مجموعه ای از تجهیزات تخصصی است که هر یک نقش مهمی در فرآیند تولید ایفا می کنند.
- میکسر (Batch Mixer): دستگاهی برای اختلاط مواد اولیه (پوکه سیمان آب و افزودنی ها) به صورت همگن. میکسرهای رایج برای بتن سبک و ملات بلوک زنی شامل میکسرهای افقی با پره های مخصوص (مانند میکسرهای پان یا سیاره ای) هستند که قادر به مخلوط کردن مواد با اسلامپ پایین هستند. انتخاب میکسر با ظرفیت مناسب و کارایی بالا برای دستیابی به ملات یکنواخت ضروری است.
- دستگاه بلوک زنی (Block Making Machine): قلب خط تولید بلوک. این دستگاه ملات را در قالب ها ریخته با اعمال فشار و ویبره آن را متراکم می کند و سپس بلوک های تازه شکل گرفته را از قالب خارج می کند. دستگاه های بلوک زنی در انواع دستی نیمه اتوماتیک و تمام اتوماتیک موجود هستند که سرعت و حجم تولید متفاوتی دارند. کیفیت ویبره و فشار اعمال شده توسط دستگاه مستقیماً بر تراکم و مقاومت بلوک تأثیر می گذارد.
- قالب بلوک (Block Moulds): قالب ها شکل و ابعاد نهایی بلوک را تعیین می کنند. قالب ها معمولاً از فولاد ساخته می شوند و باید دقیق مقاوم و تمیز باشند تا بلوک هایی با ابعاد یکنواخت و سطح صاف تولید کنند. انواع قالب برای تولید بلوک های دیواری (ته باز یا ته پر) سقفی تیغه ای و … وجود دارد.
- تجهیزات کیورینگ (Curing Equipment): مجموعه ای از امکانات برای فراهم کردن شرایط مناسب جهت عمل آوری بلوک ها پس از تولید. این تجهیزات می تواند شامل فضای مسقف برای محافظت در برابر نور خورشید و باد سیستم پاشش آب یا مه پاش برای حفظ رطوبت محیط یا اتاق ها و تونل های بخار برای کیورینگ تسریع شده باشد.
- تجهیزات حمل و نقل: مانند فرقون لیفتراک یا سیستم های کانوایر برای جابجایی مواد اولیه ملات و بلوک های تازه تولید شده و سخت شده.
- تجهیزات اندازه گیری: شامل ترازو یا باسکول برای وزن کردن مواد پیمانه برای اندازه گیری حجمی دماسنج و رطوبت سنج.
سرمایه گذاری در تجهیزات با کیفیت و نگهداری مناسب آن ها نقش مهمی در افزایش بهره وری و بهبود کیفیت محصول نهایی دارد.
مزایای استفاده از بلوک پوکه ای در ساختمان سازی
استفاده از بلوک پوکه ای در ساختمان سازی به دلیل ویژگی های منحصر به فرد پوکه و فرآیند تولید آن مزایای قابل توجهی نسبت به مصالح سنتی مانند آجر یا بلوک های سیمانی سنگین دارد:
- وزن سبک: اصلی ترین مزیت بلوک پوکه ای وزن مخصوص پایین آن است که منجر به کاهش بار مرده ساختمان می شود. این کاهش بار نیاز به سازه سنگین تر را کاهش داده و در هزینه های اسکلت و فونداسیون صرفه جویی می کند. همچنین حمل و نقل و نصب بلوک های سبک آسان تر و سریع تر است.
- عایق حرارتی عالی: ساختار متخلخل پوکه هوا را در خود به دام می اندازد و این امر باعث می شود بلوک پوکه ای عایق حرارتی بسیار خوبی باشد. استفاده از این بلوک ها به کاهش اتلاف انرژی در ساختمان کمک کرده و هزینه های سرمایش و گرمایش را کاهش می دهد.
- عایق صوتی مناسب: تخلخل بالای پوکه همچنین باعث جذب صدا می شود. بلوک پوکه ای می تواند به کاهش انتقال صدا بین فضاها کمک کند و آرامش بیشتری در محیط داخلی فراهم آورد.
- مقاومت در برابر آتش: پوکه معدنی ماده ای نسوز است. بلوک های پوکه ای مقاومت خوبی در برابر آتش دارند و در هنگام آتش سوزی گازهای سمی منتشر نمی کنند.
- مقاومت و دوام: با رعایت طرح اختلاط مناسب و کیورینگ صحیح بلوک های پوکه ای به مقاومت فشاری کافی برای کاربردهای مختلف ساختمانی دست می یابند و در برابر عوامل محیطی مقاوم هستند.
- اجرای سریع و آسان: وزن سبک و ابعاد نسبتاً بزرگ بلوک های پوکه ای سرعت دیوارچینی و اجرای کلی سازه را افزایش می دهد. برش و شیارزنی این بلوک ها نیز نسبت به بلوک های بتنی سنگین آسان تر است.
- سازگاری با محیط زیست: پوکه معدنی یک ماده طبیعی است و فرآیند تولید بلوک پوکه ای نسبت به تولید برخی مصالح دیگر اثرات زیست محیطی کمتری دارد.
این مزایا بلوک پوکه ای را به گزینه ای محبوب و کارآمد در ساخت و ساز مدرن تبدیل کرده است.
روش تولید بتن مخصوص تولید بلوک
بتنی که برای تولید بلوک پوکه ای استفاده می شود با بتن مورد استفاده در سازه های بتن مسلح یا روسازی ها متفاوت است. بتن بلوک زنی معمولاً دارای ویژگی های خاصی است که آن را برای فرآیند بلوک زنی (قالب گیری با ویبره و فشار و خروج فوری از قالب) مناسب می سازد.
ویژگی های اصلی بتن مخصوص تولید بلوک پوکه ای عبارتند از:
- اسلامپ صفر یا بسیار پایین: ملات باید سفت و کم آب باشد تا پس از قالب گیری شکل خود را حفظ کند و وا نرود.
- کارایی مناسب برای تراکم با ویبره: با وجود سفتی ملات باید قابلیت تراکم مناسبی تحت اثر ویبره دستگاه بلوک زنی داشته باشد تا فضای خالی به حداقل برسد.
- مقاومت اولیه کافی: بلوک ها بلافاصله پس از تولید از قالب خارج می شوند بنابراین ملات باید مقاومت اولیه کافی (Green Strength) داشته باشد تا در هنگام جابجایی آسیب نبیند.
- دانه بندی مناسب سنگدانه: ترکیب دانه بندی پوکه باید به گونه ای باشد که حداکثر تراکم ممکن را فراهم کرده و نیاز به خمیر سیمان را کاهش دهد.
روش تولید این بتن شامل مراحل زیر است.
- اندازه گیری دقیق مواد: طبق طرح اختلاط تعیین شده پوکه (با احتساب رطوبت) سیمان آب و افزودنی ها با دقت وزن یا حجم می شوند.
- اختلاط در میکسر: مواد به ترتیب مناسب در میکسر ریخته می شوند. معمولاً ابتدا مقداری آب و سیمان برای تشکیل خمیر اولیه سپس پوکه و بقیه آب اضافه می شود. زمان اختلاط باید کافی باشد تا مخلوط کاملاً همگن شود اما نه آنقدر زیاد که باعث تفکیک دانه بندی شود.
- بررسی کارایی: پس از اختلاط کارایی ملات به صورت چشمی یا با آزمایش های ساده مانند بررسی قابلیت شکل پذیری در دست کنترل می شود. ملات باید به صورت یک توده منسجم درآید و پس از فشرده شدن شکل خود را حفظ کند.
- انتقال به دستگاه بلوک زنی: ملات آماده شده به قیف یا مخزن دستگاه بلوک زنی منتقل می شود.
استفاده از مواد افزودنی مانند روان کننده های قوی (Superplasticizers) با دوز کم می تواند به بهبود کارایی ملات سفت و کاهش نسبت آب به سیمان کمک کند و در نتیجه مقاومت و دوام بلوک را افزایش دهد. همچنین استفاده از مواد حباب ساز یا حباب پوش می تواند به بهبود کارایی و کاهش وزن بلوک کمک کند اما باید با دقت و طبق دستورالعمل مصرف شود.
سوالات متداول در مورد طرح اختلاط بلوک پوکه ای
بهترین نسبت اختلاط پوکه و سیمان برای بلوک دیواری چقدر است؟
نسبت بهینه پوکه به سیمان برای بلوک دیواری به عوامل متعددی از جمله کیفیت پوکه نوع سیمان و مقاومت فشاری مورد نیاز بستگی دارد. به طور کلی این نسبت می تواند از حدود ۶ به ۱ تا ۱۰ به ۱ (حجمی) یا متناسب با وزن مخصوص پوکه متغیر باشد. انجام آزمایش های کارگاهی برای تعیین دقیق ترین نسبت ضروری است.
چگونه می توان مقاومت بلوک پوکه ای را افزایش داد؟
برای افزایش مقاومت بلوک پوکه ای می توانید نسبت سیمان به پوکه را افزایش دهید از پوکه با دانه بندی بهینه تر استفاده کنید نسبت آب به سیمان را کاهش دهید (با حفظ کارایی) از افزودنی های مناسب استفاده کنید و مهمتر از همه از کیورینگ مناسب و طولانی تر برای بلوک ها اطمینان حاصل کنید.
آیا استفاده از افزودنی در طرح اختلاط بلوک پوکه ای ضروری است؟
استفاده از افزودنی ها همیشه ضروری نیست اما می تواند به بهبود خواص خاصی از بلوک کمک کند. افزودنی هایی مانند روان کننده ها برای کاهش نسبت آب به سیمان مواد حباب ساز برای کاهش وزن و بهبود عایق بندی یا مواد آب بند برای کاهش جذب آب می توانند مفید باشند اما باید با دقت و بر اساس نیاز استفاده شوند.
چه نوع سیمانی برای تولید بلوک پوکه ای مناسب تر است؟
معمولاً سیمان پرتلند تیپ ۲ برای تولید بلوک پوکه ای در شرایط عمومی آب و هوایی مناسب است. این نوع سیمان مقاومت نهایی خوبی را در طول زمان فراهم می کند. در شرایط خاص ممکن است از تیپ های دیگر سیمان پرتلند نیز استفاده شود اما باید به ویژگی های آن ها مانند سرعت گیرش توجه کرد.
آیا شما به دنبال کسب اطلاعات بیشتر در مورد "طرح اختلاط بلوک پوکه ای" هستید؟ با کلیک بر روی اقتصادی, کسب و کار ایرانی، ممکن است در این موضوع، مطالب مرتبط دیگری هم وجود داشته باشد. برای کشف آن ها، به دنبال دسته بندی های مرتبط بگردید. همچنین، ممکن است در این دسته بندی، سریال ها، فیلم ها، کتاب ها و مقالات مفیدی نیز برای شما قرار داشته باشند. بنابراین، همین حالا برای کشف دنیای جذاب و گسترده ی محتواهای مرتبط با "طرح اختلاط بلوک پوکه ای"، کلیک کنید.